Quality construction is the foundation upon which infrastructure and buildings can stand the test of time, providing the most value for all stakeholders including clients, users, and the broader economy. David Akinnusi, Quality Manager at leading black-owned contractor Concor Construction, highlights that this principle is at the core of the company’s build-to-last philosophy. With its track record of more than 150 years of construction experience, Concor continues to imbed quality through its depth of expertise and dedication to quality assurance and quality control (QA/QC), says Akinnusi.
“Looking back at the iconic landmarks we have built over the decades, our commitment to this philosophy is well proven,” he says. “These mega-structures range from the Greenpoint Stadium in Cape Town and Pavilion shopping centre near Durban and the mega Menlyn Mall, to our current work on the Msikaba River bridge in the Eastern Cape.”
He highlights the key elements of Concor’s quality control systems as being its detailed systems and procedures which ensure operational standardisation across all projects. The company puts designated QA/QC personnel on each project, to monitor and ensure compliance to internal and external requirements and specifications.
“At the planning stage, for instance, our contract directors and estimating teams undertake detailed tender reviews – to fully understand the project’s resourcing, scheduling and costing requirements,” he explains. “Drawings are then generated at design stage for construction by professionally registered engineers, with collaborative efforts to identify and address any constructability concerns.”
Strict quality control plans are also compiled for the execution stage and agreed upon by the contractor and client. These plans outline the specific testing and inspection that is required for the different trades employed for each project. This attention to detail continues through the handover stage, when the structures are handed over to clients through trade data book reviews.
“Our clients are contractually allowed to snag the works to ensure handover is done to their satisfaction,” he says. “A contractual defects liability period is applied to each project and, depending on the latent defect root cause, Concor remedies defects that arise during the liability period.”
Concor applies a rigid non-conformance system that determines root causes of defects, as well as corrective and preventative measures. Post-project reviews are conducted to ensure that lessons learnt are effectively captured and applied to the next project. The company is also transitioning to digital inspection systems for improved efficiencies and data analysis.
Akinnusi emphasises that Concor’s quality regime is aligned with world class industry standards, including being certified in terms of the ISO 9001 quality management standards. This keeps its management systems in line with the highest international requirements; it does the same in the fields of health and safety (ISO 45001) and environmental management (ISO 14001).
“These standards ultimately give effect to the quality of structures we build for our clients,” he says. “We are also members of well established and credible construction industry bodies such as the Master Builders Association, the Construction Industry Development Board and the Green Buildings Council of South Africa.”

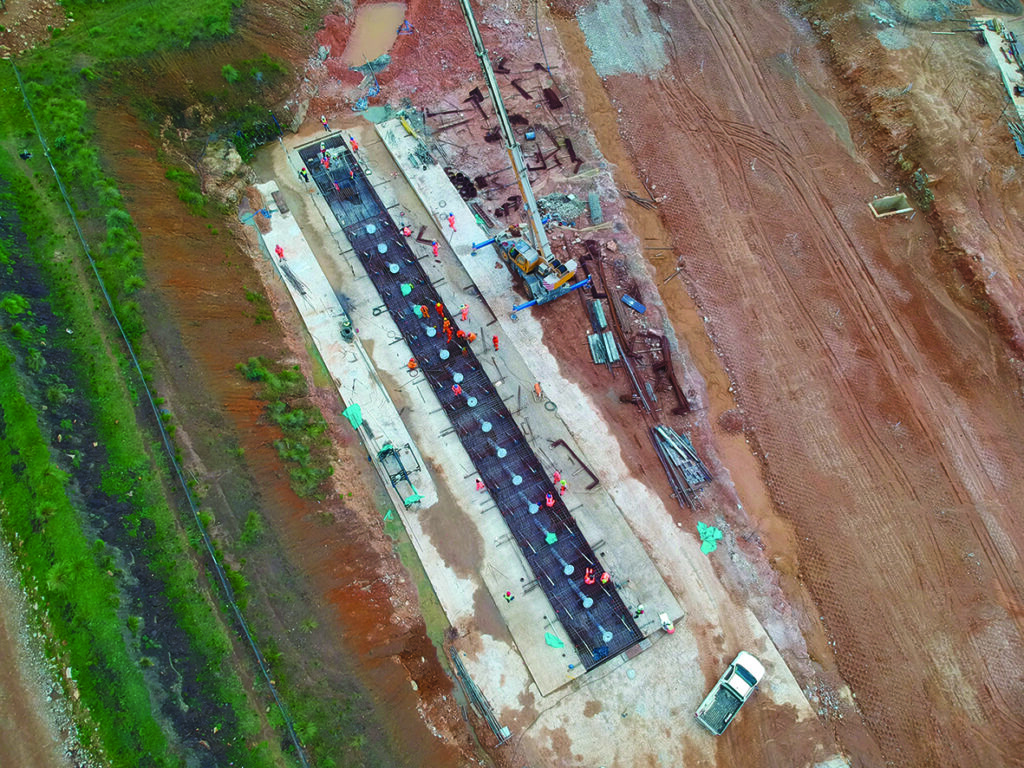
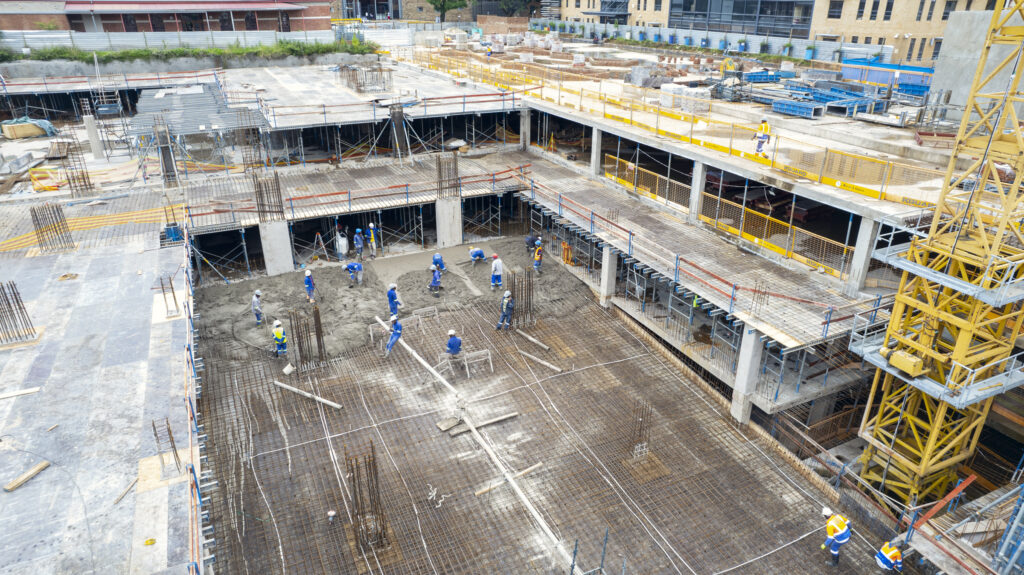
Quality control forms an integral part of the Kendal Ash Disposal Facility project.
Quality control during anchor block installation at the Msikaba Bridge Project was very important.
Work on the Trevenna Super Basement project was undertaken applying stringent quality control processes.