Modern day plastics have improved to the point where they are able to outperform traditional materials in a myriad of applications and even withstand high loads and abrasive conditions. Polymer technology in products like igus’ igutex fibre composite technology is able to withstand extreme loads in heavy-duty applications. With advancements in polymer technology, the application boundaries for technical plastics have expanded significantly.
Motion plastics specialist, Juan-Eric Davidtz of igus South Africa says as a result polymers have gained widespread use in various industries. It easily replaces steel or bronze in loads exceeding 100MPa. This is where companies like igus have been at the forefront of developments with new thermoplastics with fibre reinforcements boasting impressive strengths in real-world scenarios.
“In the real-world materials face alternating, unevenly distributed and dynamic loads that impact them in multiple ways. Forces can act simultaneously in different directions or induce fatigue and stress due to frequent changes in intensity and direction.
“Therefore addressing high-load scenarios requires a multidimensional approach surrounding factors beyond just material compressive strength, but also shear strength, toughness and creep resistance are equally crucial attributes that must be considered, says Juan-Eric. As a result our researchers and engineers have turned to high-performance polymers and formulations, utilising flexible injection moulding processes and harnessing fibre composite technology.
“With over four decades of experience in plain bearing development we have perfected our igutex TX3 material for this kind of heavy load application. These bushings utilise extremely strong filaments woven together to absorb high loads effectively. By embedding solid lubricants for friction reduction and lubrication-free operation, igutex combines mechanical stability with high load-bearing capacity,” says Juan-Eric.
He explains that fibre composite technology offers a fresh perspective especially when traditional injection-moulded plain bearings reach their limits. Like the thermoplastic iglidur materials, igutex TX3 allows for tailored properties through recipe changes in the fibre composite technology. The material’s shape and processing method can be influenced, resulting in materials well-suited for various requirements. This development not only enhances resistance to high loads but also provides a new level of performance in heavy-duty applications.
While high-strength fibre composites exhibit unparalleled strength values, injection moulding holds its ground as a potential cost-effective solution, particularly for large quantities. igus maintain dedicated teams of engineers to explore the capabilities of injection-moulded thermoplastics. The iglidur Q3E, a multi-layer plain bearing exemplifies this approach, combining various optimised iglidur materials to perform different tasks. With high-load applications no longer confined to solid steel or bronze bearings igus is redefining the possibilities of high-performance polymers.
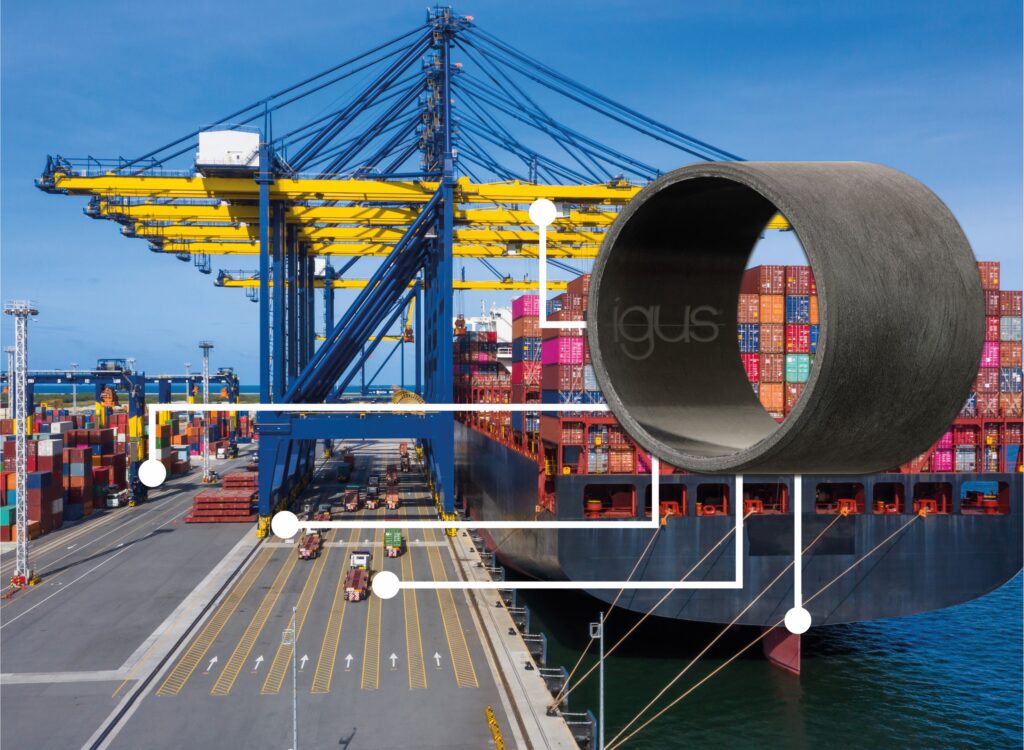