SA Gauge, a proudly South African B-BBEE company founded in 1992 by Chris and Judith du Plessis, has become a stalwart in the field of pressure and temperature measurement. In memory of Chris du Plessis, who passed away in 2021 at the age of 61, SA Gauge’s journey reflects a legacy of determination and vision. From humble beginnings of handcrafting gauge scale plates with Judith, the company has grown into a prominent force in the industry, boasting two self-owned branches in Johannesburg and Head Offices in Durban that houses the SANAS-accredited laboratory with both branches manufacturing precision instruments.
The company’s commitment to excellence has amassed over 30 years of expertise in designing and manufacturing pressure and temperature gauges as well as a range of related accessories, diaphragm seals and pressure testing kits. In industries where conditions can be challenging and demanding, the company demonstrates its dedication to quality through its comprehensive range of heavy-duty pressure gauges and inert gas-filled dial thermometers. These gauges are manufactured in compliance to EN 837-1 standards, designed to endure rigorous conditions while maintaining precision and the utmost quality. Each gauge comes with a distinctive two-year guarantee, a rarity in the South African industry. According to Judith du Plessis, the Managing Director, this guarantee underscores the company’s dedication to delivering instruments of unparalleled durability and accuracy thus becoming a trusted name across various industries namely, the industrial, mining, chemical, hygienic and process industries.
SA Gauge’s calibration laboratory offers both calibrations accredited to SANAS ISO/IEC 17025 standards and an in-house calibration service not only to its own brand but to all brands of pressure and temperature gauges. The laboratory guarantees a swift two-day turnaround time for pressure calibration and a three-to-four-day turnaround time for temperature calibration certificates. As industries continue to evolve, SA Gauge remains at the forefront, providing instruments that meet and exceed the stringent demands of the sectors requirements providing internationally traceable accuracies to uphold the highest standards in the industry.
The company’s extensive in-house manufacturing capabilities, encompassing both conventional and advanced technology has allowed the company to streamline manufacturing of components with high accuracy, accommodating both large orders and small, specialized requests, even for non-standard items. By maintaining control over the production process in-house, SA Gauge ensures the high standards and timely availability demanded by all industries eliminating dependence on third-party contractors. Customization remains a speciality in OEM orders manufactured to customer specifications with short lead times for special dials and custom logos. What sets SA Gauge apart is its handcrafted and individually calibrated instruments, by competent and adept employees providing a level of reliability that is second to none.
A paramount principle of the company is to educate customers on optimizing operational efficiency with the use of pressure and temperature gauges. The company emphasizes considering all process and ambient factors during selection and installation, providing guidelines to prevent gauge failure. Specific considerations such as working pressure, wetted parts compatibility, temperature, corrosive and solidifying media, vibration, pulsation, overpressure, installation practices, and calibration intervals and more are provided. SA Gauge highlights the importance of early detection and prevention in ensuring precision, safety, and avoiding unplanned downtime, process issues, and subpar product quality. A well-maintained and calibrated gauge is crucial for accurately indicating system performance and averting accidents, equipment damage, and injuries.
The country’s unstable electricity supply has necessitated an investment in solar systems which became fully operational in both branches as of August 2023. 10 kw Solar systems were installed for the Johannesburg branch to keep critical systems online during load shedding as well as 100 kW to the Durban branch, with 70kW solar array, which runs most of the manufacturing facility, with plans to increase the production of the system in the future. Thus, as SA Gauge looks to the future, its commitment to customer satisfaction and continuous efforts to minimize costs to end users remains a top priority.
SA Gauge’s journey is a testament to its founders’ vision and the collective efforts of a dedicated team, ensuring the company’s continued success in the dynamic field of pressure and temperature measurement.
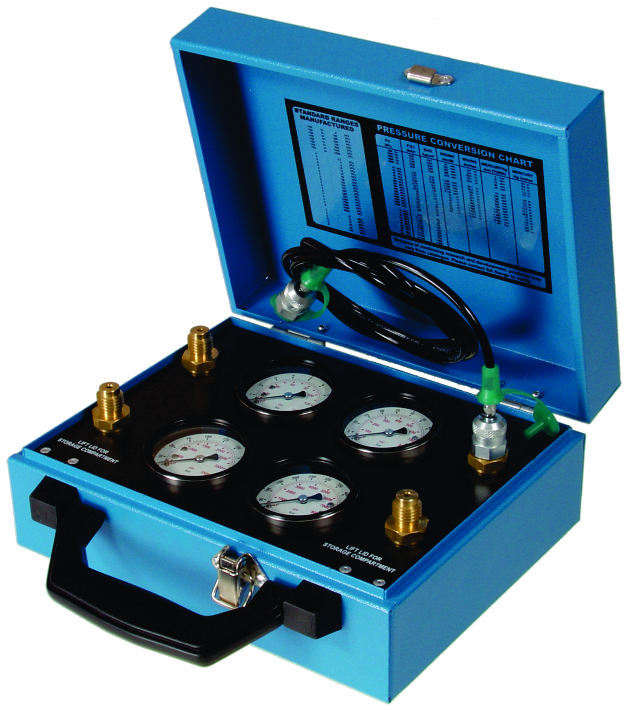
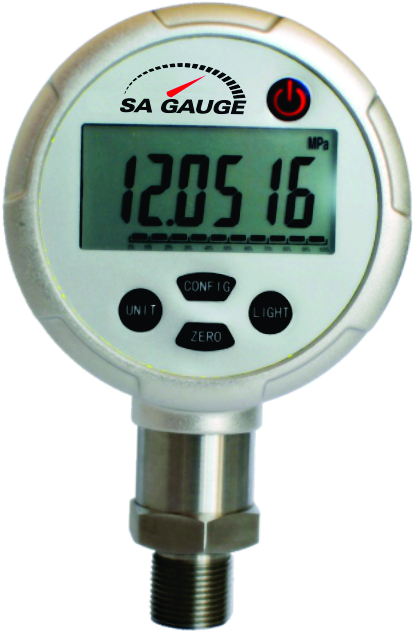
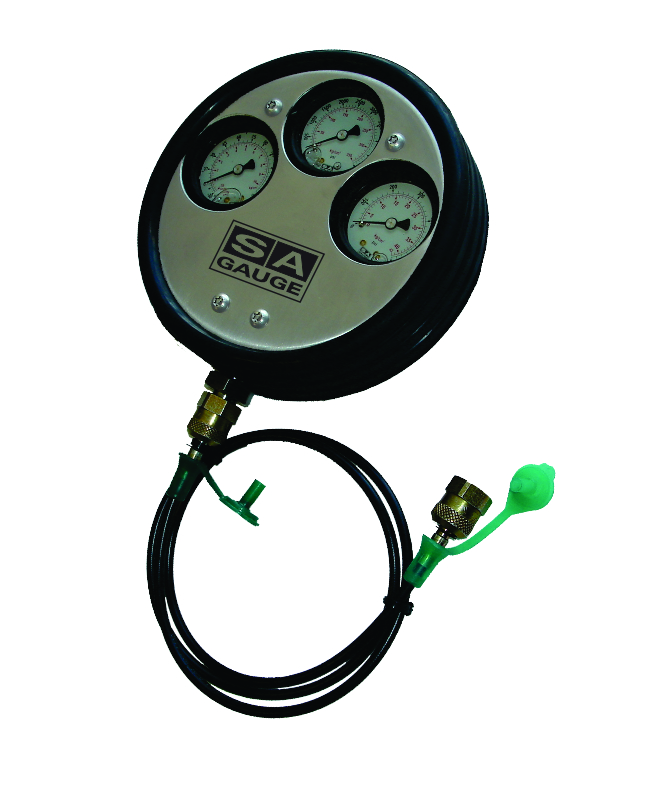