Zinc is a versatile metal with a wide range of applications, including die casting. Die casting is a high-volume production process that can produce parts with complex geometries and tight tolerances. It is versatile and can be used to produce a variety of components. The manufacturing process uses high pressure to force molten metal into a mould.
Zinc die casting is widely used in the automotive industry and other sectors needing complex and durable components. Examples of zinc die cast parts are door handles, fuel pumps, brake components, connectors, housings, and gears.
Being relatively inexpensive, zinc is a good material for die casting. It has good casting properties and is recyclable. Zinc die casting involves several steps: The mould cavity is made from a steel or aluminium die, into which molten zinc is pressure forced. The zinc solidifies and cools and the part is then ejected from the mould.
A major advantage of using zinc in die casting is that it produces castings with good dimensional accuracy. Zinc has a low melting point and a high fluidity, so it flows easily into a mould. Zinc castings are also strong and durable and can be used in a variety of applications, explains Simon Norton, Director of the International Zinc Association (IZA) Africa.
“Another advantage of using zinc in die casting is that it is a relatively inexpensive metal. It is a cost-effective option for many manufacturers. Zinc is also recyclable, so it can be reused without having to extract new metal from the ground. This makes it an environmentally friendly choice,” highlights Norton.
Here are some specific examples of the role of zinc in die casting:
- Zinc is used to make die casting alloys, which are mixtures of zinc with other metals such as aluminium, magnesium, and copper. These alloys have improved properties, such as strength, ductility, and machinability.
- Zinc is used as a core material in die casting. Cores are inserts placed in the mould to create hollow or intricate features in the casting. Zinc cores are lightweight and easy to machine, making them a good choice for many applications.
- Zinc is used as a coating for die castings. Zinc coatings protect the casting from corrosion and improve its appearance.
The most common type of zinc used in die casting is ZAMAK, a family of alloys with a base metal of zinc and alloying elements of aluminium, magnesium, and copper. The name ZAMAK is an acronym of the German names for the metals of which the alloys are composed: Zink (zinc), Aluminium, Magnesium and Kupfer (copper).
ZAMAK alloys are part of the zinc-aluminium alloy family, differentiated from other ZA alloys due to their constant 4% aluminium composition. It has good strength, hardness, and corrosion resistance properties making them ideal for a wide range of applications.
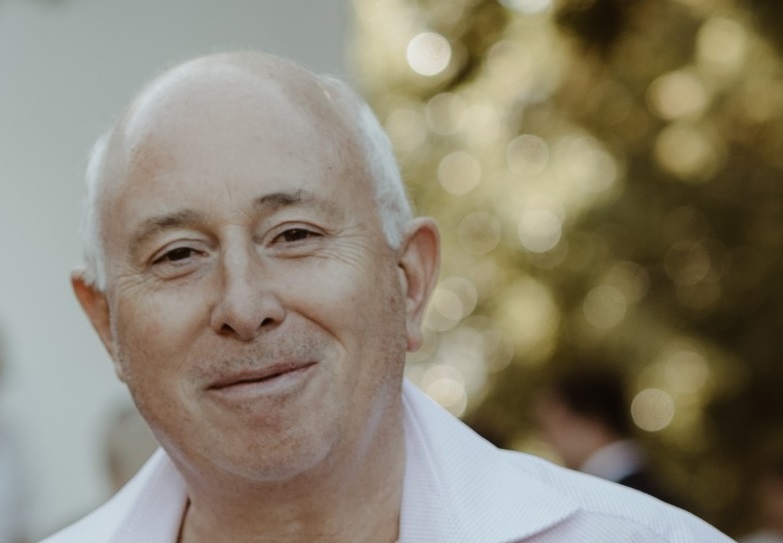