“It is becoming increasingly important to maintain food integrity and to do what we can to minimise food shortages. The devastating effects of droughts, floods and fires, show food insecurity to be a major concern globally. Every one of us in agriculture and industry has an important role to play in making a difference during this time of crises and uncertainty,” says Ken Mouritzen, Manager, BLT WORLD. “One of our most critical responsibilities, is to preserve the quality of food products in every stage after harvesting. The use of substandard or incorrect grain handling equipment results in kernel damage and deterioration of the grain and seeds. Large grains, like corn, can be particularly susceptible to physical damage during handling and is more vulnerable to fungi and insect infestation.
“Dust is a major problem associated with conveyor systems in all sectors, particularly where workers have prolonged exposure to the hazards of dust particles. Apart from the negative effects of dust on one’s health – like irritation to the eyes, skin and respiratory tracts, as well as serious lung diseases – some types of dust can also form an explosive mixture with air, which is extremely dangerous.
“It is therefore crucial that the correct conveyor skirting is used to offer maximum safety to workers and to ensure minimal deterioration of foods and to maintain the desired level of quality.”
Specialists in post-harvest processing are continually looking for more efficient, dependable systems to alleviate problems associated with product damage in bulk handling. It is also important for industry to be able to cope efficiently with the challenges of handling moist and sticky materials.
Common difficulties of bulk conveyor systems include dust, spills and contamination at the transfer points of conveyor systems. Misalignment, abrasion and subsequent belt damage are other problems in food conveying.
The BLT WORLD team has installed a highly-effective system on a conveyor system at a food production plant – comprising the ScrapeTec AirScrape, TailScrape and PrimeTracker belt tracker – and feedback from the customer is positive.
Extreme dust development at the plant caused damage to belt components, due to jamming and spillage. In addition, friction from dust caused wear and tear on side and rear seals, allowing the escape of materials and dust.
According to the plant manager, since the installation of the ScrapeTec system over three years ago, dust levels around transfer points are significantly reduced, ensuring a safer and healthier working environment. In addition, running costs are lower because there are no longer the costly energy requirements of extraction fans. This highly-effective system also minimises the risk of explosions at critical sections along the conveyor route and transfer points – an important safety feature. The plant manager also notes there is reduced need for extensive cleaning operations and maintenance work on the conveyor belt is minimal.
Prior to this installation at the plant, the team had to spend hours each day, cleaning the belt periphery and all transfer points, from unplanned material spills and the remnants of product. The plant manager had previously tried various methods to cope with costly material spills in the plant’s moist and sticky environment, without success. This efficient conveyor system enables the team to now spend more time on productive work at the plant.
Studies in other projects show, that even after five years after installation and with continuous use in harsh conditions, BLT WORLD’s ScrapeTec systems hardly show any signs of wear. Operational costs are also reduced because there is no need for high energy consumption, spillage collection, regular maintenance, or replacement parts.
The contact-free AirScrape conveyor belt skirting system is a highly-effective side seal that lies over the conveyor belt, without contact, and creates negative pressure on the belt, due to its specially-designed blade structure. Because this system hovers freely above the conveyor belt, skirt friction and belt damage are eliminated and service life of every component of the conveyor is extended.
Conventional skirting is pressed against a conveyor belt to keep dust and material in the middle of the belt, but after a period, wear of the skirting and belt can be so severe, that material and dust are able to escape. The danger is fine wear particles can be ingested by workers and consumers.
Material spillage at transfer points needs to be removed at great effort and cost and regular maintenance of belt skirting and transfer points is necessary.
The durable ScrapeTec system consists of non-flammable and anti-static polyurethane materials and blades made from Stainless Steel. FDA-approved materials are also available for specific conveyor handling applications.
DustScrape consists of a durable filtering cloth that is installed above the conveyor belt, to retain dust particles created by conveyed materials, while remaining permeable to circulating air. This long-lasting filter cloth, with cleaning and dust-releasing properties, is available with different qualities, including anti-static features, for specific applications – for example, in surface or underground mining. The dust retaining filter cloth, which is manufactured in rolls, can be extended to any required length and is suitable for any conveyor belt width.
It is notable that DustScrape and AirScrape operate without energy consumption, which means operational costs are signficantly reduced.
The TailScrape system enhances performance of the AirScrape, by sealing the transfer tail in the rear area and also works according to the Venturi concept, to prevent dust generation and material spills. The intelligent blade structure on the underside of the system, creates negative pressure in the conveying area, preventing the escape of materials. Dust is kept in the material flow by air intake.
Also in the range of ScrapeTec conveyor components, is the PrimeTracker belt tracker, which eliminates other problems associated with conveyor belt systems, including misalignment, abrasion and belt damage.
Correct installation of suitable equipment ensures cost efficiency, optimum performance and safety, reduced risk of breakdown and extended service life of the conveyor system.
BLT WORLD’s advanced solutions for conveyor systems are designed for use in diverse sectors, including the handling of difficult bulk materials, like corn and feeds, cement, fertilizer, coal and minerals.
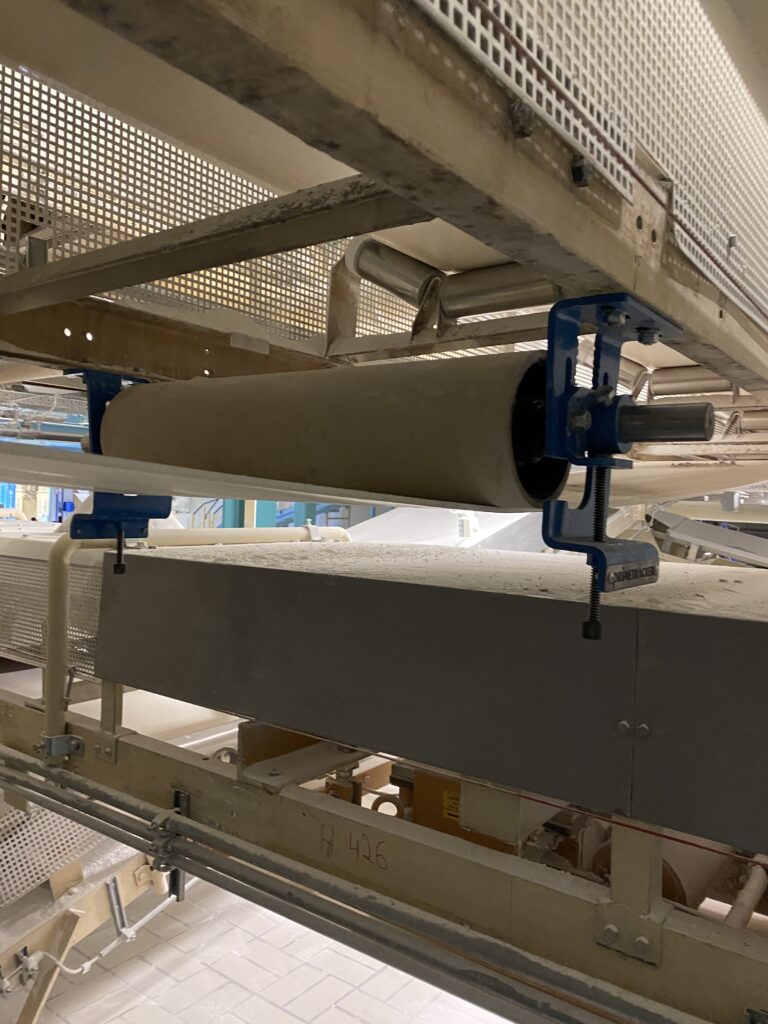

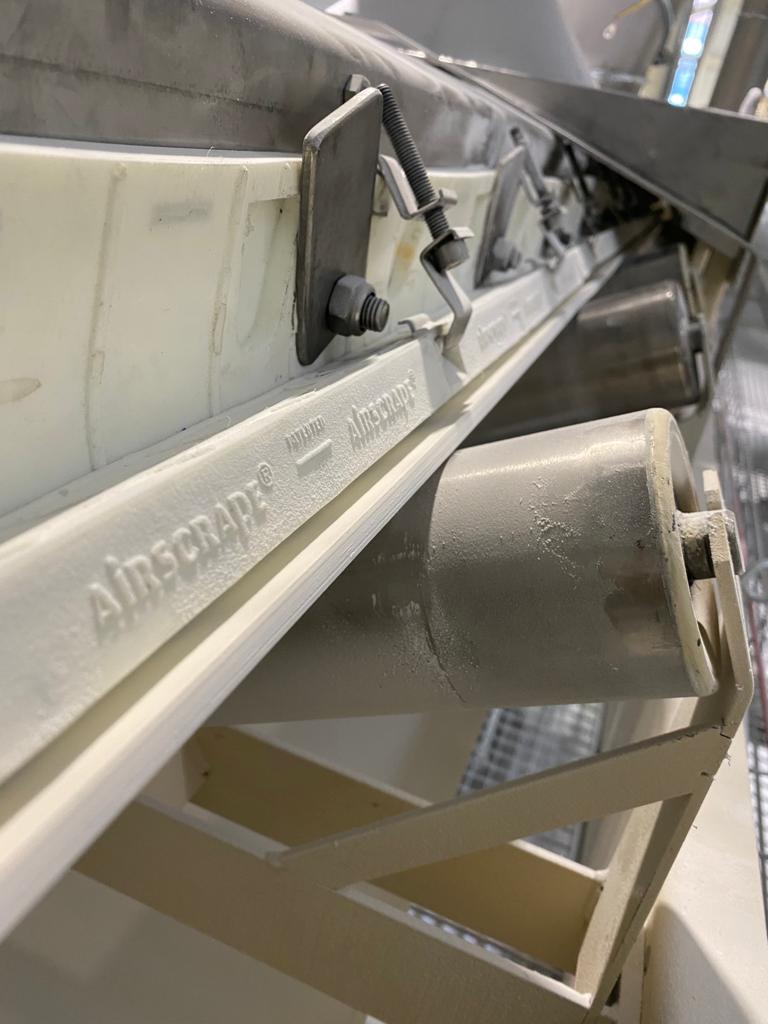
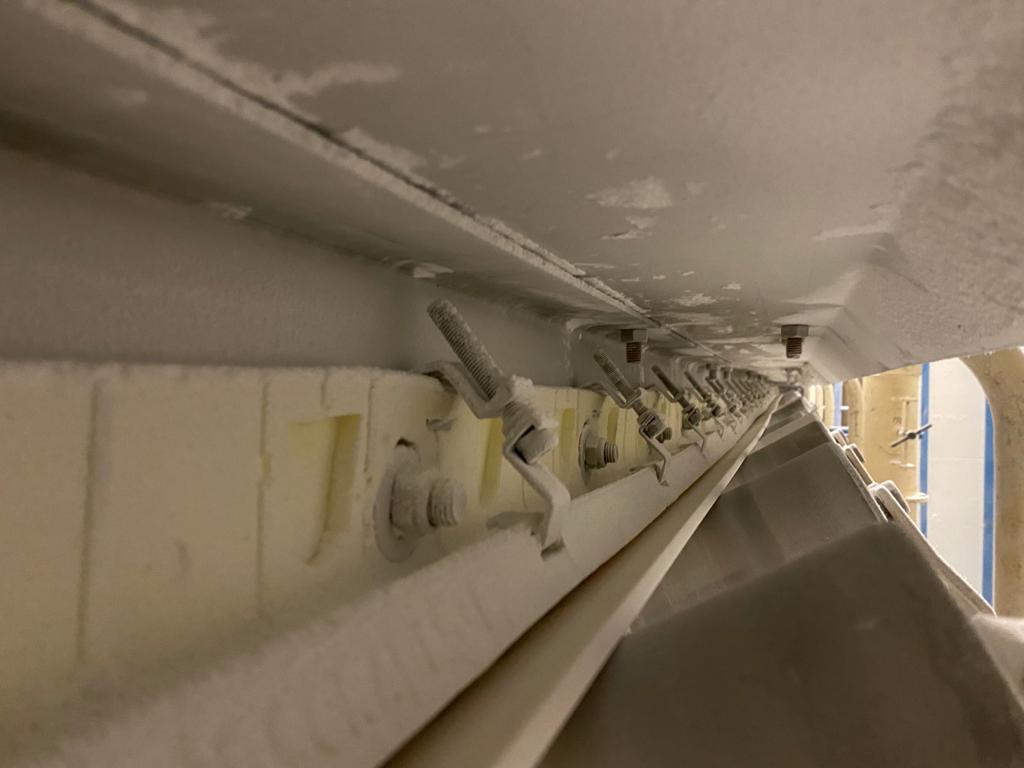