As a demolition specialist with a global project footprint, Jet Demolition has had the privilege of undertaking some of the most challenging projects in the world, resulting in being crowned ‘Best of the Best’ at the World Demolition Awards (WDA) 2020, competing against colleagues from the US, Canada, and Australia.
Being acknowledged as ‘best of the best’ was a career milestone for founder and director Joe Brinkmann, who undertook his first blasting course and underground blasting work in the US over 40 years ago.
Brinkmann’s first large demolition project in South Africa was at the Old President Brand Gold Plant in Welkom for Anglo American. He had first approached the mine to sell explosive charges but was then asked to undertake the turnkey project instead. “This was our first foray into the heavy industrial demolition space,” comments Project and Contracts Manager Kate Bester.
From there, it was a natural progression into more difficult and demanding demolition projects. A hands-on approach, mechanical interest and aptitude and a fondness for explosives came together to fuel Brinkmann’s drive for demolition work. His passion and love for demolition filters throughout all aspects of the company, resulting in a team with a true drive for demolition.
“We realise and appreciate recognition is fleeting, and that the true strength of the company resides in its people. What makes Jet Demolition so special is how our team inspires each other to continue learning, developing and growing from strength to strength,” says Bester.
“It is a reminder yet again that amazing things can be achieved by a team with a unified goal. I continue to be in awe at what can be achieved when people elect to actively face adversity and use challenges as opportunities to grow.”
Jet Demolition has been fortunate to be able to hone its implosion skill, culminating in its three most challenging projects to date, as outlined below:
Supertech Twin Towers in Noida, Utter Pradesh, New Delhi
The implosion on 28 August 2022 was a collaboration with Edifice Engineering, a leading demolition company based in Mumbai. The successful implosion of the Apex and Cayenne towers (103 m and 97 m respectively) followed India’s Supreme Court ruling ordering the illegal structures to be demolished. Apex was unique as it was the tallest building ever to be imploded in India, and one of the top 15 tallest buildings to be imploded globally.
The detailed planning and implosion preparation was especially challenging due to the close proximity of the towers to neighbouring buildings, in addition to their robust construction to be able to withstand high-magnitude earthquakes. Test blasting revealed that unusually high explosive loading was required to reliably fail the shear walls. These shear walls fell into the class of ‘highly unforgiving’ when it came to attempts at explosive-driven rupture.
Due to the 3 516 kg of explosives required to successfully fell the structures, the impact and potential for structural damage to surrounding buildings was a significant concern. There was heightened anxiety among authorities and stakeholders that the adjacent building at a mere 9 m away, beset with structural degradation, would be further weakened and collapse from implosion-induced vibration.
Dozens of columns were strengthened, beams were back-propped, and an array of crack gauges installed to monitor prominent structural cracks – but no movement or crack growth was induced by the implosion. Nearby buildings were draped with geotextile curtains to minimise window breakage.
Minimal superficial impact, with a small number of windows cracked and an 8 m section of brick boundary wall to contend with after the implosion was an extremely satisfying result. Following the successful implosion, Edifice Engineering and India joined the 100 m implosion club under extremely demanding conditions. “This project also saw our first foray into navigating the streets of New Delhi on a scooter – even more exciting than the implosions themselves!” notes Bester.
Maradu region of Kochi in Kerala, India
The implosion of the Apex and Cayenne towers (103 m and 97 m respectively) followed on from Jet Demolition’s previous successful collaboration with Edifice Engineering in January 2020, when three high-rise structures were imploded within 24 hours in the Maradu region of Kochi in Kerala, India. It marked its first foray into India and the first time that a high-rise building in that country was demolished by implosion.
The three high-rise apartment buildings were the 20-storey Holy Faith H2O, the 18-storey Jains Coral Cove, and the 16-storey Golden Kayaloram. The former was imploded successfully on Saturday 11 January 2020, while the latter two were imploded successfully on Sunday 12 January 2020. All three buildings were located within 1.5 km of each other.
The major concern of the Indian authorities was the safety of the public in this high-density area and surrounding properties, the closest being a school only 6 m away from Golden Kayaloram. The solution to protect the school was to effectively split the 16-storey building into two, thereby collapsing it in two directions, avoiding and preserving the school building.
Initial ground investigations revealed that the structures had been built on alluvium in a designated wetland area. This meant that the magnitude of the ground vibrations induced by the implosions was sufficiently low not to cause any damage to surrounding buildings.
Another major challenge was the fast-track nature of the project. Due to the fact that an urgent demolition order for the three buildings had been issued by the Supreme Court of India for violating building regulations, Jet Demolition only had 2.5 months from inception to successful completion. The fast-track project saw the team work 12 to 16 hours a day, seven days a week, interspersed by the occasional game of street-cricket.
With safety being paramount during the implosions, extensive layers of wire mesh and geotextile cover was placed around the columns where the explosives were fixed, acting as source protection to contain the rubble. Secondary protection included hanging perimeter curtains on the façades of surrounding buildings in order to contain the dust that was generated.
A total of 600 kg of cartridge explosives was used, as well as 31 000 m of detonating cord and 5 300 blast holes. Due to the tight timeframe, diamond-drill coring was not feasible. Instead, electric percussion drills were used for drilling charge holes in selected and strategic positions, such as the lift-shaft walls.
Some 800 national and 300 local police personnel oversaw the evacuation process and traffic control on the day of the implosions themselves. Everything went very much according to plan. “A project of this complexity, within this timeframe and to this level of detail would not have been possible without the dedication, co-operation, and support from all stakeholders,” says Bester.
Bank of Lisbon, Johannesburg
In the central business district of Johannesburg, South Africa, Jet Demolition successfully imploded its tallest-ever reinforced concrete frame building on 24 November 2019. This was the 108-m-high, 31-storey Bank of Lisbon building.
“It was one of the most complex projects we have ever undertaken. We were also highly conscious and respectful of the fact that three firefighters lost their lives when a fire broke out in the building in September 2018,” highlights Bester.
Jet Demolition was awarded the contract after a competitive tender process and presented our main client, the Gauteng Department of Infrastructure Development (GDID), with two options: Controlled implosion of the entire structure, or a top-down mechanical demolition process. Given the sensitivities surrounding the site itself, and concerns about the extent of damage to the structure, GDID opted for implosion.
The first step was to re-support the fire-damaged steel-reinforced concrete building by installing engineered propping with an advance-warning monitoring system to warn of any creepage that could indicate an imminent collapse. Thereafter all the furniture, contents and fixings for the three government departments that had occupied the building, as well as the personal property of the building occupants, had to be removed for off-site storage, for which a man-and-materials hoist was installed.
Jet Demolition carried out a geotechnical investigation, design and installation of lateral support to the basement retaining walls to ensure their stability during, and after, demolition. The fact that there were no structural drawings available for the building meant it had to physically determine the make-up of the compromised structure and the exact location of services such as electricity, water and fibre-optic cabling.
The main building columns tapered quite dramatically from the bottom to the top, which required a detailed assessment of the column size and rebar strength at all points. The columns were at their widest in the basement at 1.5 m by 1.8 m. Breaking up these massive columns posed a major challenge, especially as all debris had to be contained to prevent damage or injury. The closest building was only 7.8 m away.
The team ended up blasting various structural elements on 14 floors in order to guarantee a high level of the explosive-induced collapse process. It was necessary that the rubble fold into the tightest, most compact form on the way down as it was deposited into the basement, where impact cushions were installed to minimise ground vibration.
An extensive electronic blast initiation system was installed so that each of the 2 363 separate charges could be individually timed and perfectly sequenced in accordance with the implosion design. An important part of the blast design was to spread the detonations as far as possible within the timespan required to set off all the charges.
A total of 914 kg of conventional mining and civil engineering explosive was used in the implosion. The charging process itself took nine days to complete, beginning the week prior. Implosion protection curtains were hung 25 m high to protect the building façades from any flying debris.
A total of over 60 000 m2 of geotextile fabric, as well as 1 600 rolls of diamond-mesh fencing, was used for containment. The implosion took place at about 09:03. “From the time that the first charge went off, to everything being down on the deck, was a thrilling eight seconds, culminating in the most challenging implosion project we have undertaken to date,” concludes Bester.
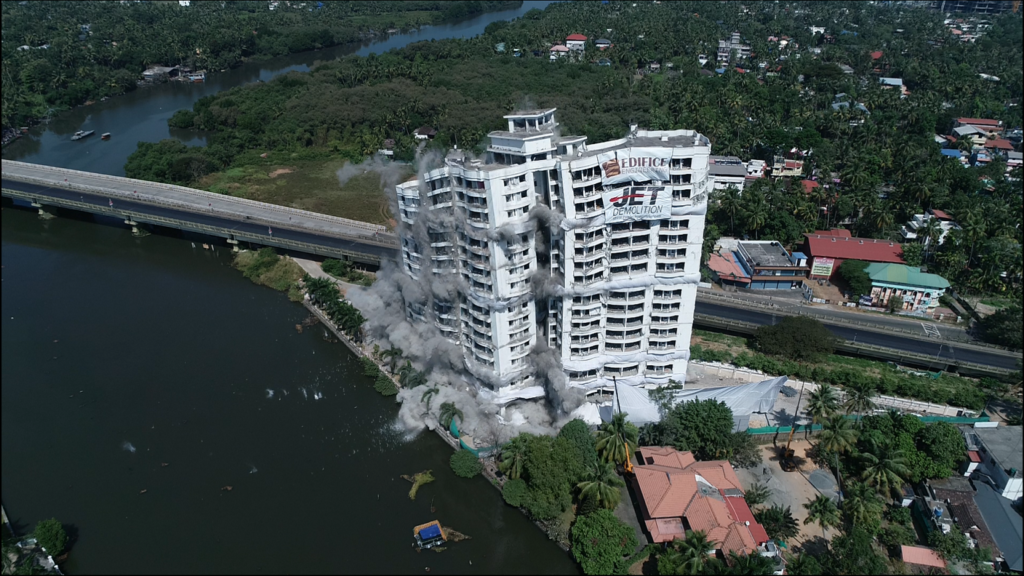
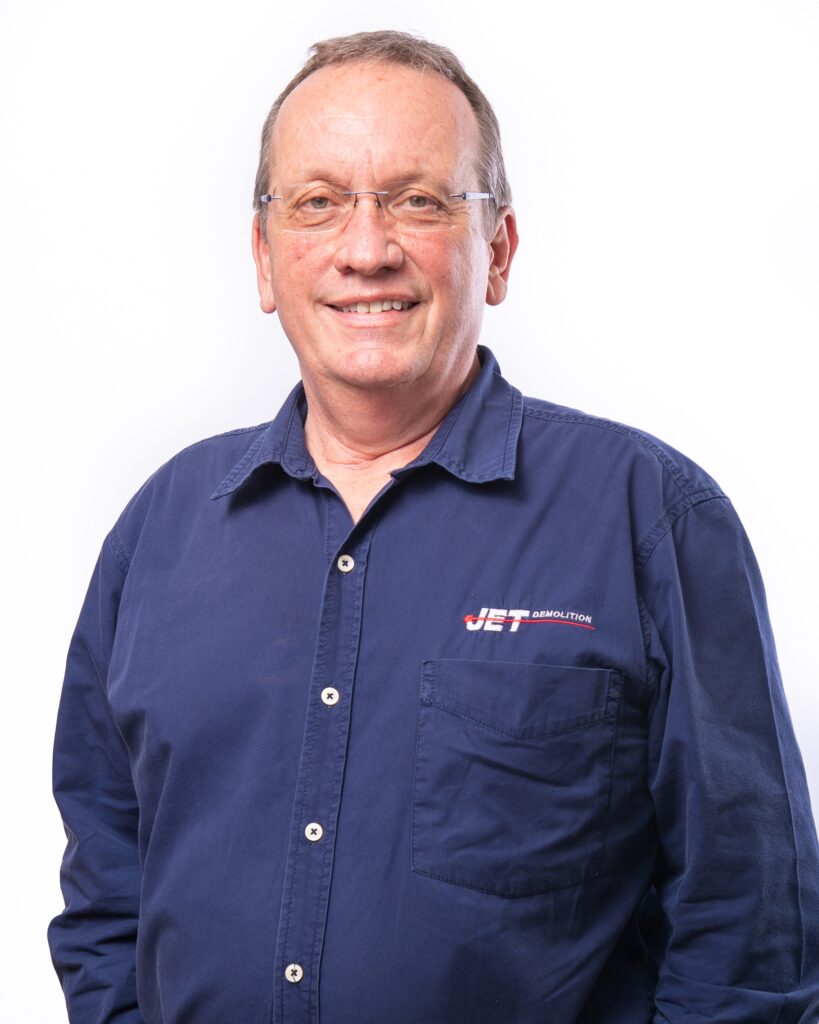
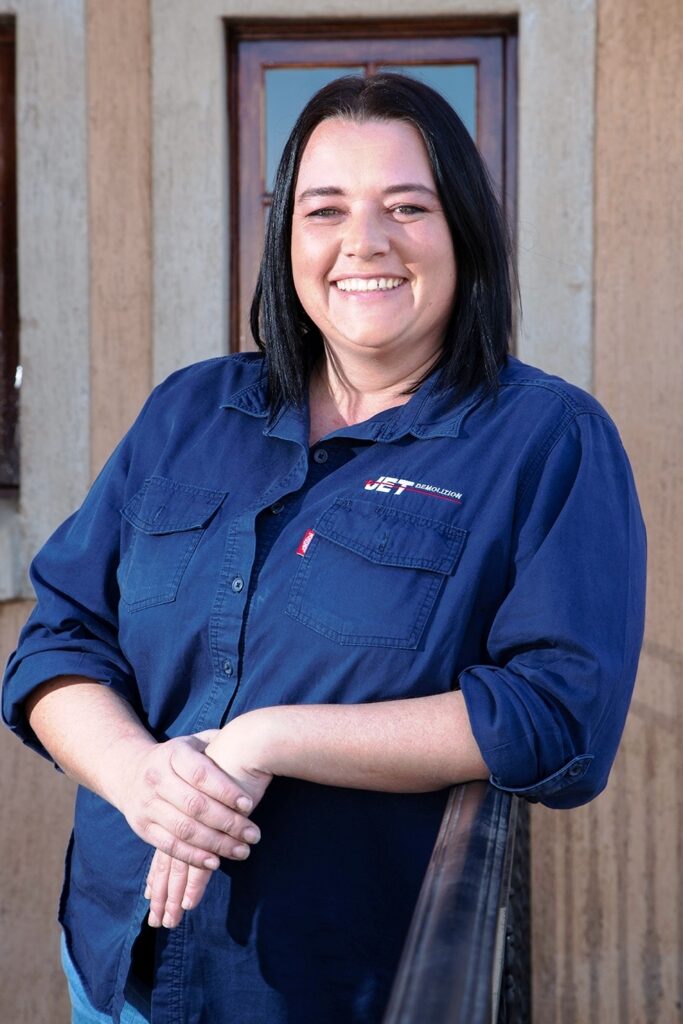